Made Possible by Continuous Evolution
13 January 2025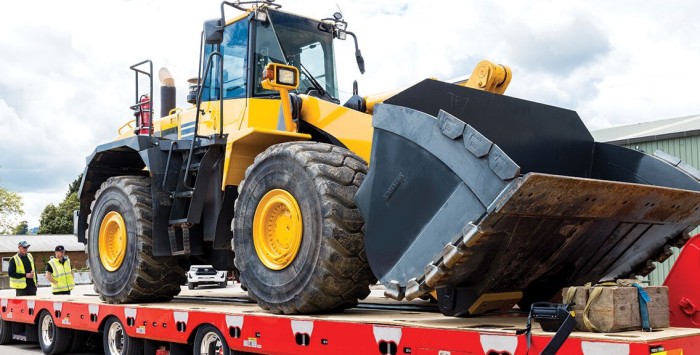
Credit: Cranes & Lifting Magazine
Evolution is a continuous process at TRT and when they’ve made their best version, they make it better. Every generation of TRT trailers builds on the innovative design engineering that came before it. The team at TRT recently staged a customer event focused on a new trailer design.
TRT’S engineering and design team have spent the last 12 months refining the design of the new 4 x 8 dedicated ESS Low Loader. The design is a New Zealand specification, new Low Loader build that uses TRT’s patented Electronic Steering System technology and follows in the footsteps of its successful ESS Platform and House Trailers. Jeremy Carden, TRT Trailer Sales, explains more.
“For some time now, TRT has seen the need for an all-steering Rows of Eight Low Loader in the NZ market. The design is new but the TRT team has simply tapped into the ESS Platform design and worked out where the tare weight can be removed, while at the same time maintaining the strong chassis shape and construction. This reduction in tare weight enables the new trailer to be highly competitive within the NZ heavy haulage market.
“Over a period of time we’ve undertaken a number of changes and updates to the design and general construction of the trailer. We are now in a position where we can manufacture a four-line platform trailer with the same dimensions that previously weighed 30 tonne. The newly designed trailer comes in at 22.5 tonne, providing customers with a 7.5 tonne payload increase.
The customer benefits are numerous explains Jeremy.
Image/TRT
• A competitive tare weight, allowing for increased payloads
• Reduced running costs – rubber stays on the rim.
• Massive advantages in manoeuvrability due to an active, intuitive steering system, along with an increased suspension stroke.
“Customers with a four-line lead platform trailer require a dolly in the mix to be legal on the road, whereas with the new trailer, for at least 50% to 60% of the time, the customer will be able to remove the dolly from the equation,” Jeremy said.
“Dollies don’t steer and are generally regarded as a difficult piece of equipment to operate, so eliminating the dolly is a significant benefit.
“Another benefit in New Zealand, more than in Australia I’d say, is non-steering trailers in the heavy-haulage market have been the norm for many years. In regards to the maintenance of the running gear, customers are constantly wearing through tyres, breaking them off the bead and generally placing heavy strain on the trailer leading axles and the trucks chassis.”
“Another huge benefit of the ESS system design is the suspension stroke. In comparison to standard rows of eight, the new build features three and a half times a suspension stroke, which means it’s going to be a lot more user friendly on uneven terrain,” said Jeremy.
“The idea of having a trailer that is not ‘fighting’ you as you navigate corners and roundabouts because it’s actively steering behind you, has seen a large number of customers purchase our ESS Platform Trailers which has been a huge step forward in the New Zealand market,” said Jeremy.
“Kiwis are a very progressive bunch, our roads aren’t getting better any time soon, so our trailers need to be constantly evolving as the loads tend to get larger and longer.”
ESS technology is very similar to that seen in modern all-terrain and mobile cranes, enabling the trailer to actively steer behind the truck, says Jeremy. The driver can override the auto-steering as long as the truck is at an offset angle, this can be done right up to 50km/h and is probably the biggest advantage to this ESS system overall.
“Our ESS trailers follow the truck’s arc through a turn and have a pivot point that can be adjusted. Like all-terrains, our trailers can crab sideways behind the truck and can basically mirror the truck’s angle. Having been the Grove distributor since 1972, none of this technology is new to us and we’ve basically developed this technology in our trailers.
In terms of software development, our partner is Bosch Rexroth with the ‘brain’ or the ‘beating heart’ of the trailer being the Rexroth controllers or RC controllers, which are mounted in an enclosure on the side of the gooseneck,” said Jeremy.
“As long as the operator has configured the trailer correctly, as the truck moves off at a different angle, it causes a rotation in the slew ring up on the fifth wheel coupling, and that transfer of angle is picked up by mechanical cogs that are mounted to two encoders inside the teeth of the slew ring.
That information is then communicated through the controllers with signals being sent via CANBUS to the individual steering rams,” he said.
THE TRT CUSTOMER DAY
“For a live demonstration trailer event in New Zealand, the Customer Day was very well attended. The majority of customers in NZ are smaller owner-operators, whereas in Australia our customers tend to be larger companies,” said Jeremy.
“We were really pleased to see between 30 and 40 customers in attendance, and we had 15 of our staff on hand to talk about the development.
We also had a number of customers attend from the South Island, which was really impressive. The Customer Day included a static display of the trailer and staff were able to highlight the various features and benefits, but customers really wanted to see the steering.
“We were able to demonstrate how the integration between the truck, the operator and the trailer work into one cohesive unit. We demonstrated how the remote control can override the steering and how to use the truck to dictate the crab steering. I think everyone was impressed with what they saw,” said Jeremy.
“We are actively building large modular ESS platform trailer systems for companies that require this type of technology, and at the moment, it seems to be in high demand from crane companies in particular – these include Borger’s, Max Services, Pollocks Cranes and Qube Heavy Lift.
“There are plenty of others that are seeing the advantages of our trailers because of the amount of infrastructure work they are involved in. For many of these projects, the lifts are in tight and confined areas and the ESS technology is ideal for these applications.
“The next step for Australia isn’t going to be a four by eight, it will be a five by eight ESS low loader. On the east coast of Australia especially, it’s going to be a lot more useful and that design will be ready over the next six to 12 months,” said Jeremy.